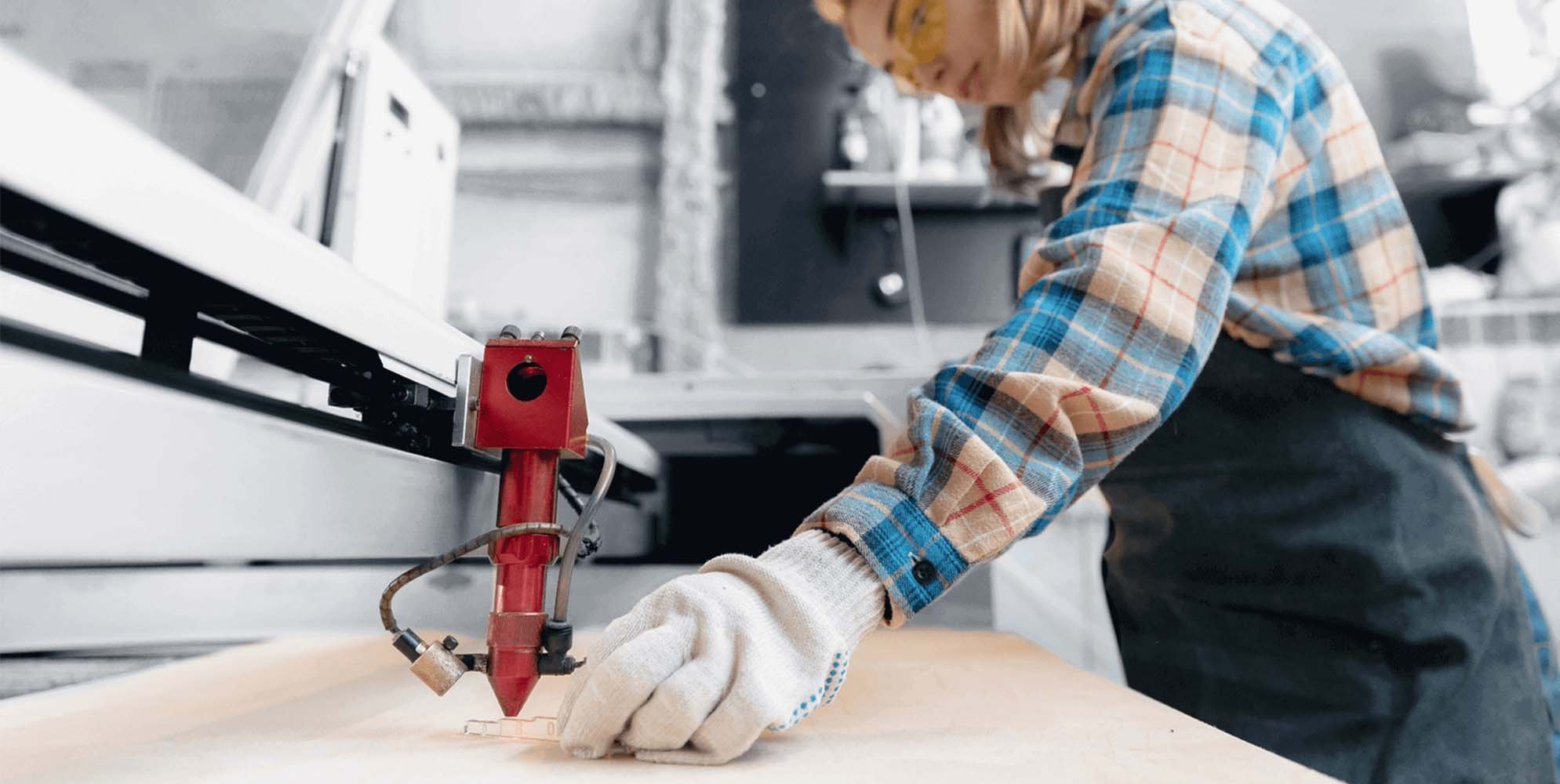
CO2 Laser Service Packages
Providing Affordability, Empowering Performance, Minimal Downtime
Whether you are a creative, business, school or university, nothing is more frustrating than suddenly facing an issue with your laser machine, bringing operations to a standstill and generally resulting in a costly callout from an engineer at your busiest time.
Our laser machine service packages offer comprehensive support and peace of mind as you embark on your journey with CO2 laser technology. Enjoy year-round technical assistance, an annual machine service as standard, priority on-site callouts, and substantial discounts on replacement parts.
Let's unlock the full potential of your laser system! Please fill out the form below, alternatively, call or WhatsApp us on 01271 626 406 for a quick response.
Beyond Repairs. Proactive Maintenance for Laser Longevity.
FAQ's About Our CO2 Laser Machine Service Packages
Curious about our service packages? Check out our responses to common questions our customers have asked over the years, or feel free to contact our engineers directly. We're happy to help!
-
Our service packages are popular amongst various industries across the UK. They are ideal for creatives, schools, universities, and businesses looking to avoid any additional costs while maintaining and getting the most out of their laser machine.
All our service packages are adaptable and can be tailored to meet your specific requirements.
-
During your annual site visit from our engineers to service your CO2 laser, we'll carry out various machine maintenance tasks and safety checks to ensure your machine is operating in optimal working conditions.
Laser tube health check including a power wattage test
Complete optical alignment of the laser tube, mirrors, and mirror mounts
Bed level adjustment
Belt checks and re-tensioning
Check and clean all mirrors and lens
Replacement / top-up of chiller unit water
Linear rails and bearing checks
Proximity sensor and safety interlocks check
Electrical system health check
Calibration and adjustment of machines software to ensure maximum efficiency
Finally, our engineers will carry out a test cut / engraving to ensure the machine is performing optimally. We'll also provide a full report of the work carried out, include any recommendations when operating your laser system and give you a heads-up on any potential replacement parts that may be required in the near or foreseeable future.
-
We offer technical support through various channels, including whatsapp, email, and remote access tools, ensuring you get the help when you need it most. Here's what it typically covers
Assisting with identifying and resolving machine errors
Diagnosing issues with software, hardware, or communication
Guiding users through troubleshooting steps and potential solutions
Answering questions about machine setup and configuration
Advising on optimal settings and parameters for processing different materials
Providing guidance on laser alignment, optics cleaning, and machine maintenance
Helping with software installation, updates, and troubleshooting
Explaining software features and functionality
Assisting with design import and file preparation
Providing recommendations for replacement parts
Offering guidance on laser safety and best practices
-
Our engineers have the experience of working with a wide array of laser cutter brands. While we can't provide an exhaustive list, some of the common brands our service packages cover include:
Boxford
CTR Laser Cutters
Epilog Laser
HPC Laser / Laserscript
Lotus / Blu series
Mantech / Lasertech
Burghmann
Omtech
Opus
Thunder Laser
Universal Laser Systems
Is your laser cutter brand not listed? Please contact us directly, and we'll be happy to confirm if we're able to help support your make and model of Co2 laser.
-
Going for a service package is a win-win situation for all laser machine owners. It keeps your maintenance costs predictable, so there are no nasty surprises there. Additionally, the annual servicing of your laser system will keep your laser machine in tip-top working condition and help schedule preventative maintenance at a convenient time.
But the best part? You get that awesome peace of mind knowing your laser cutter is in great condition, and if you do run into any issues, you have a team of experts just a phone call away.
-
We recommend having your laser machine serviced annually, but this does depend on use. In some instances where a machine is utilised 24/7 we have clients that like to get this done every 3/4 months, others choose a 6 month interval, most common is a yearly interval, and some prefer a 1.5 year interval as the machine is only used on occasion.
It’s important to choose the correct service interval based on your use as regular servicing is vital to preventing unexpected breakdowns, minimising downtime, and prolonging the lifespan of your laser cutter.
If you aren't sure which schedule would suit your machine the best just get in touch and we would be happy to advise.
-
The lifespan of a laser machine depends on several factors, including its build quality, usage frequency, maintenance practices, and the type of laser source.
DC (Glass) laser tubes have an average lifespan of 4 years depending on the quality, usage and maintenance. Whilst RF (Metal) laser tubes have a typical lifespan of around 7 year
Additionally, let's remember that while the laser tube is a crucial component, other parts like optics, motors, and electronics can also wear out over time. Regular maintenance and timely replacement of worn components can help extend the overall lifespan of your laser cutting machine, and ensure the machine and all components are not only able to work optimally together, but also reduce the levels of stress on any one given component needing to perform harder to compensate for another worn component.
We've all heard of the old saying, you get what you pay for; well, it couldn't be more true when it comes to CO2 laser cutters. On average, you can expect a well-maintained laser machine from a reputable supplier to last anywhere from 5 to 15 years or even longer.
-
The cost of training varies based on factors such as the duration, location (on-site or remote), and specific training needs. Please get in touch with us for a personalised quote.
-
Yes, we provide ongoing support and assistance even after the training is complete.
Additionally, we also offer a range of service packages that include an annual service as standard, remote technical support, extensive discounts on replacement parts and callouts from our engineers.
You can contact us with any questions or issues that arise.

Processing Tips.
Tips for maximising your laser machine: achieve precise engraving, clean cutting edges, reduce processing time and more.